SCREENS
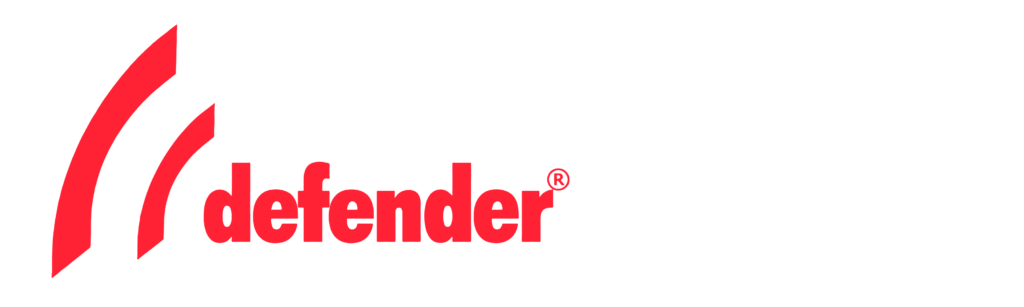
Static and Rotary Drum Screens for Wastewater Pretreatment
Toro Equipment’s Defender® screens are designed to optimize the first stage of pretreatment in industrial and municipal wastewater systems, ensuring accurate and efficient removal of solids. Available in both static and rotary drum versions, these screens adapt to the specific flow rates, solid loads, and installation needs of each facility.
Manufactured with high-strength materials like 316L stainless steel and optional GRP reinforcements, Defender® screens are built for continuous operation in demanding environments, offering long-term durability and low maintenance. Their automatic high-pressure cleaning system in rotary models reduces manual intervention and maintains efficiency over time.
Defender® screens are available with perforated or wedge wire mesh and in different sizes to ensure optimal performance under varying operating conditions. They protect downstream processes by effectively separating solids at the head of the treatment line.
What Makes Defender® Screens Different?
Rotary and static models available: Adaptable to different space, flow, and solids conditions
Optional TR-Smart® system: Intelligent control with frequency inverter adjusts drum speed based on solids load, minimizing energy use and maximizing autonomy
Custom configurations: Multiple mesh types and sizes to ensure high separation efficiency in a wide range of applications
Reliable and low-maintenance: Designed for continuous performance and minimal operator intervention
The Defender® screen range is designed to meet a wide variety of flow rates, space limitations, and solids loads, ensuring effective pretreatment from the very first liters.
MODELS
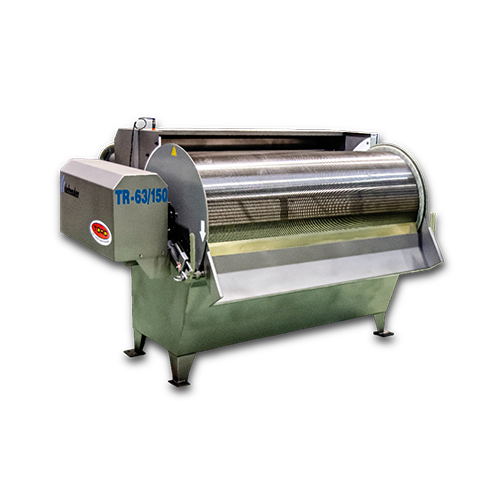
Rotary Screens (TR)
Capacity
From 7 m3/h up to 363 m3/h in clean water
Small flow rates
High performance with high solids load
Smaller filter surface
Description
Produces polished effect, high output water quality
Protected from outlet overloads
Robust, high strength infused GRP lamella construction
Easy to clean.
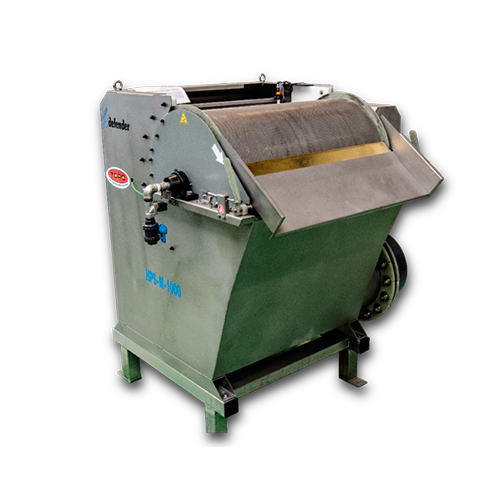
Rotatory Screens With High Pressurisation System (HPS)
Capacity
From 133 m3/h up to 5864 m3/h
Description
Produces polished effect, high output water quality
Protected from outlet overloads
Solid construction using high-strength infused FRP lamellas, ensuring no collapse.
Easy cleaning
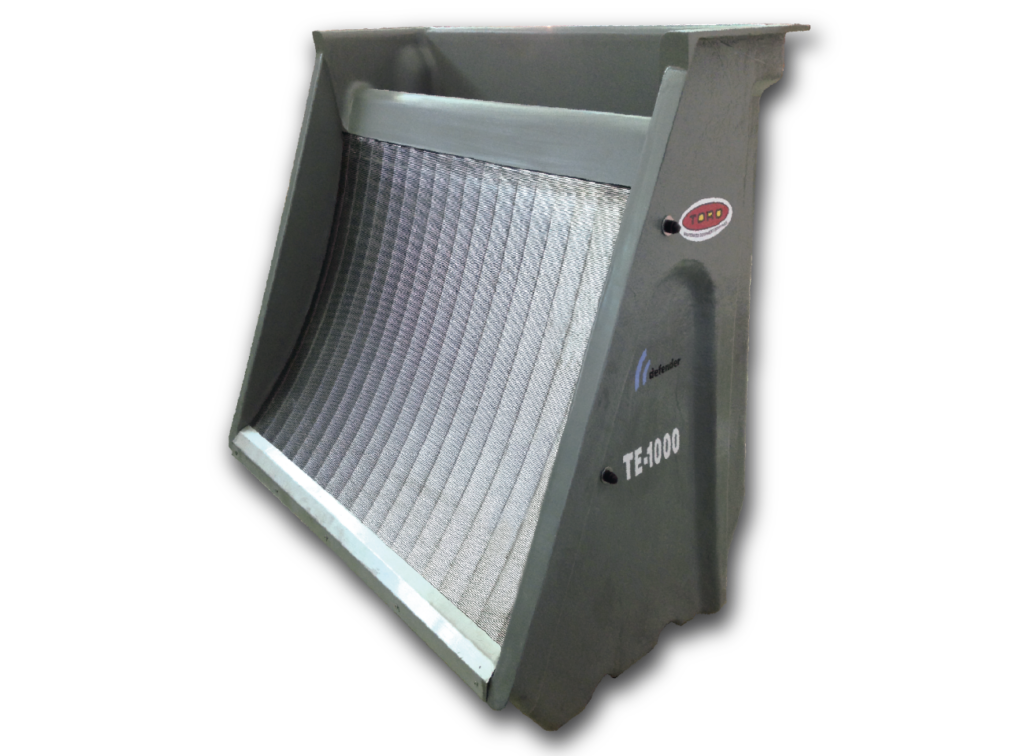
Static Screens (TE)
Description
Its mission is to eliminate the solids carried by the water, in order to avoid clogging and mechanical problems in the installations.
This equipment requires little maintenance and operates continuously, without the need for electricity.
In urban waters, they can replace primary decanters in many cases, providing the elimination of coarse sands and up to 30% percentages of grease and effluent leftovers.
MODELS OF MESHES
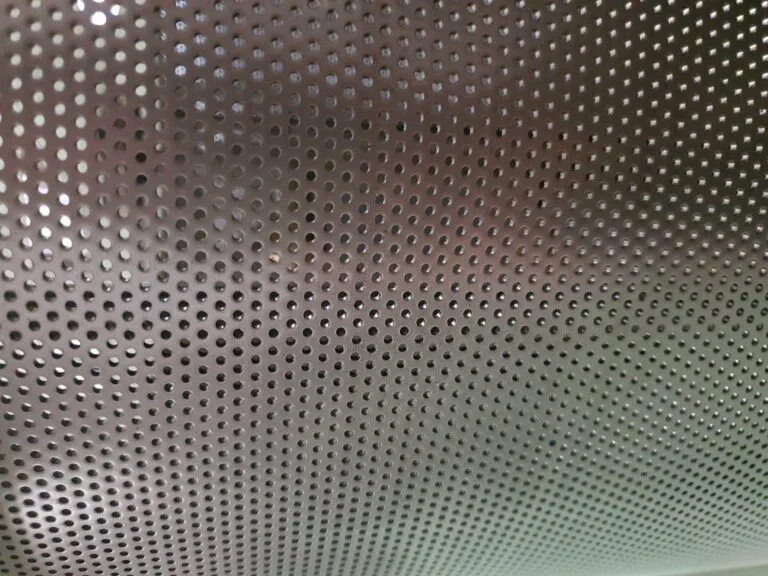
PERFORATED
Mesh size from 2 to 3 mm Ø
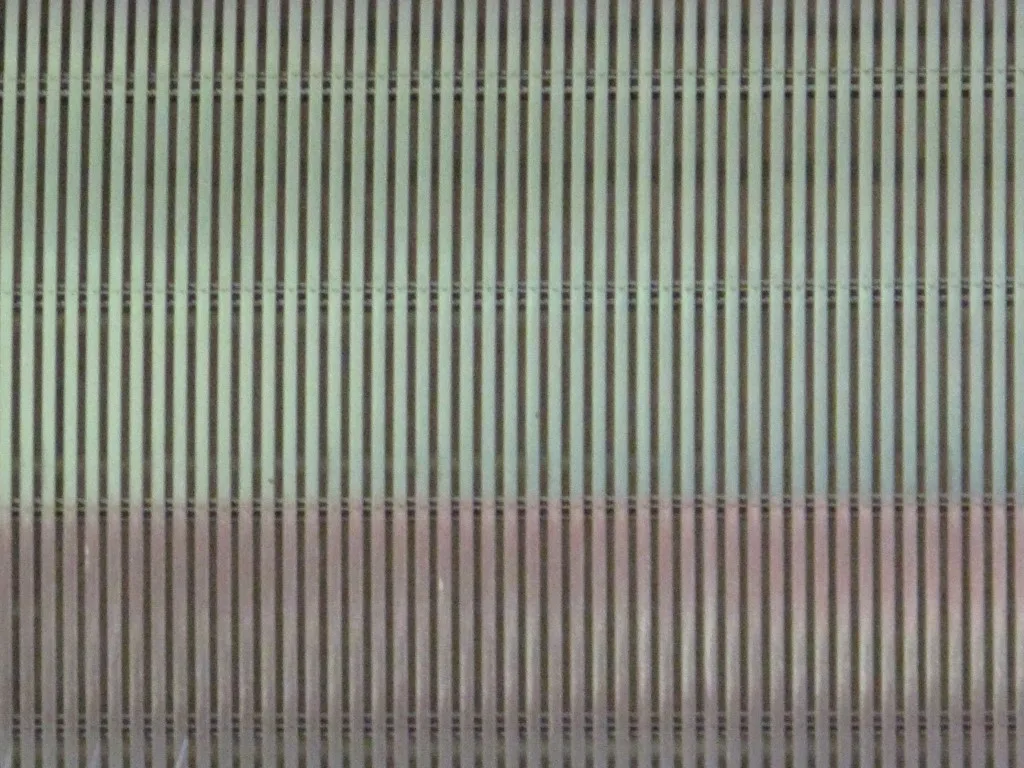
GRID
Mesh size from 0.15 to 2mm
OPERATION
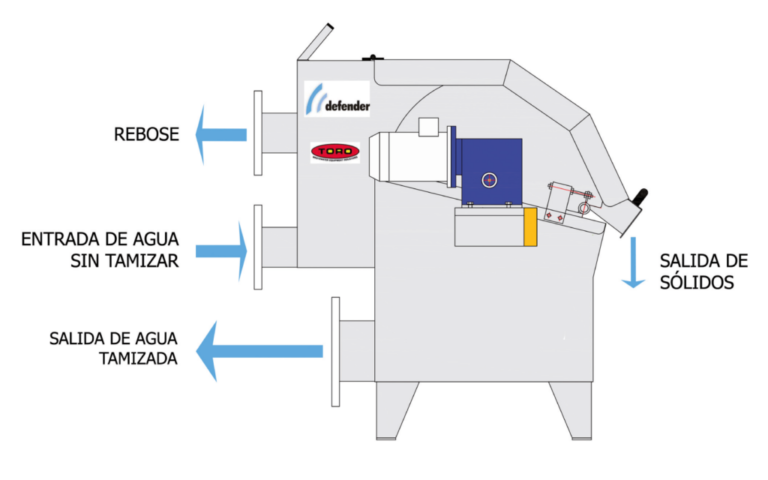
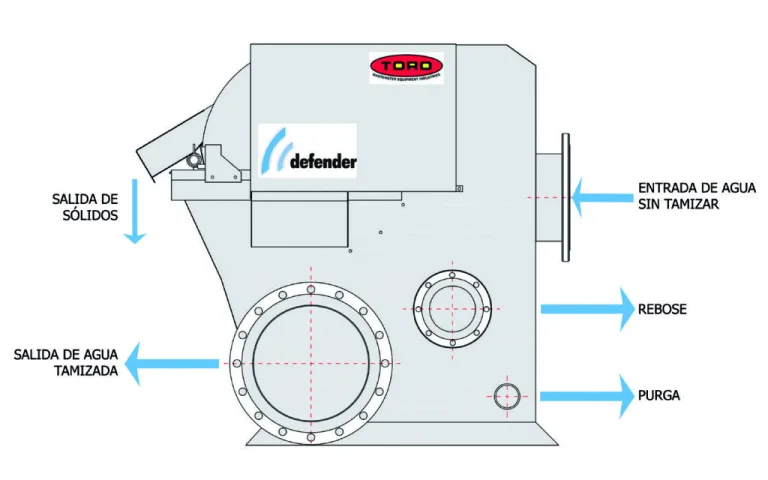
ROTARY SCREEN
The effluent to be treated enters through the flange on the outside of the screen body and is evenly distributed through the spillway and overflow through the filtering drum
The solids are retained on the surface of the drum while it is rotating, the spill penetrates through the mesh opening and performs a self-cleaning function by passing through the lower part of the drum again
As it passes through the outer scraper, the solids are released from the screen and gravity causes the solids to fall off the scraper
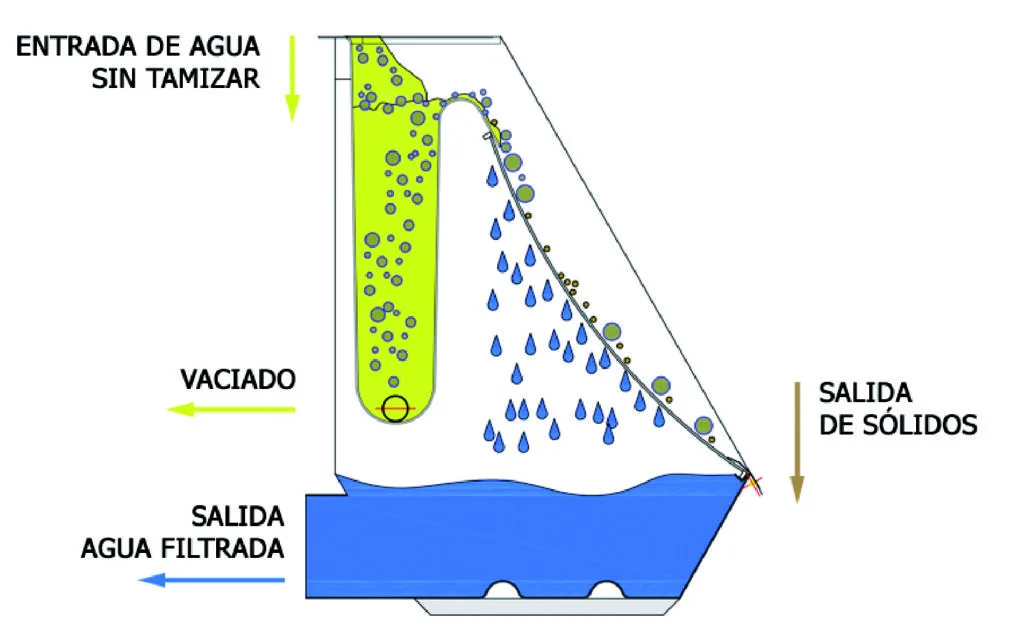